Finished Projects
Please check out the projects below to get a general sense of the types of projects, designs, and ideas we can help with.
These are just some examples, the possibilities are endless!
Solvi the Faering

The sail is a Dacron faux canvas made in Essex England, enlarged 23% over the design to 125 sqft. She had 3 reefs and we used them all often enough, from light air to 35 knot gusts. It was a great sail.

It's hard to find a hull form that will both row and sail with decent performance. In rowing, speed is arbitrary, but Solvi could really move along with her 19' waterline and fine ends.

Solvi, renamed Solveig, crossing from Seattle to Victoria.

The sail is a Dacron faux canvas made in Essex England, enlarged 23% over the design to 125 sqft. She had 3 reefs and we used them all often enough, from light air to 35 knot gusts. It was a great sail.
This faering designed by Chesapeake Light Craft's John Harris took us over 2,500 miles from St. Croix Falls, WI to Grand Isle, LA via the Mississippi and Atchafalaya River systems. Designed for stitch and glue plywood, the design had too much shape, which made it too difficult for the home builder and so was never put into a kit. We chose to add decks for increased safety and storage. Building in western red cedar strips instead of plywood saved 100lbs. over the plywood version empty hull weight. Solvi went on to be the smallest boat to complete the R2AK in 2019- a challenging motor-less race over 700 miles up the famous Inside Passage: Seattle to Alaska.
Gulf and Bay Enterprises




For the 2 years I was in school I worked for Gulf and Bay. Gulf and Bay is 3 companies: Dock Works, Dock Wraps and Divers. I started in the field leading a crew of divers and eventually finding my role as warehouse manager, purchasing agent and project designer. This company is a family and I have been a part of it in one capacity or another for over 3 years now. These are some of the projects I have designed for them. Dimensions have been removed to protect content or only the customer drawing has been shared.
A New Cockpit



The benches fit with the layout with the boat. Many people thought they came with the boat, and were not added separately!

When we bought the Benbow Cutter, Sirocco, she had beautiful teak splash boards in the cockpit. These were great to look at but woefully nonfunctional for passages or ports, because you could not sit on them, or lean against them comfortably. The benches were designed to maintain a clean aesthetic, but add the functionality a small boat needs. Sit on them, sit against them, straddle them and put your things in them, these benches changed the cockpit for the better in a big way.
Airstream Renovation




When we got cabin fever during the COVID lockdown, stranded a thousand miles away from our home (Sirocco), we decided there was nothing to do but Keep On Keeping On and to renovate an old airstream to get us back on the road. We started by fully gutting the neglected 1965 Land Yacht's interior and exterior of old coatings/materials. Once we had our freshly coated aluminum shell, complete with all new windows, screens and roof vents. We then installed tinned wiring (soldered/shrunk) and PEX plumbing throughout. We went with a modern interior design based on the latest Airstreams available, but tailored to our self sufficient and "simple is reliable" ethos. 50 gallons of fresh water, 390W of monocrystalline high voltage solar, a 12 sq. ft. rear door/window, a ready heat water heater, LED's and 4 low draw fans, are really the main features of this project. In typical K&D fashion, KOKO was completed start to finish in only 6 weeks.
Teardrop

I designed this teardrop for my wife and I to use during our road trip from WI to Florida via the Rocky Mountains.



I designed this teardrop for my wife and I to use during our road trip from WI to Florida via the Rocky Mountains.
We were sailing the western coast of Costa Rica and as hurricane season approached we knew we needed to go back to WI and retrieve our car and Solvi's trailer. I took that opportunity to design a modular and ruggedly simple composite teardrop camper. Being a prototype built on a tight budget, little Sunny the Teardrop was a composite sandwich of 1.5" Styrofoam and sheathed in 1/4" plywood. This large amount of insulation made the small space comfortable from the shores of The Great Salt Lake in mid-summer to the cold passes of the Colorado Rockies. Sunny was a big step up from a tent with fans, lights, roof vent, running water (5gal), and an efficient cooking area with protection from sun/rain.
Hollow Beam Longboard
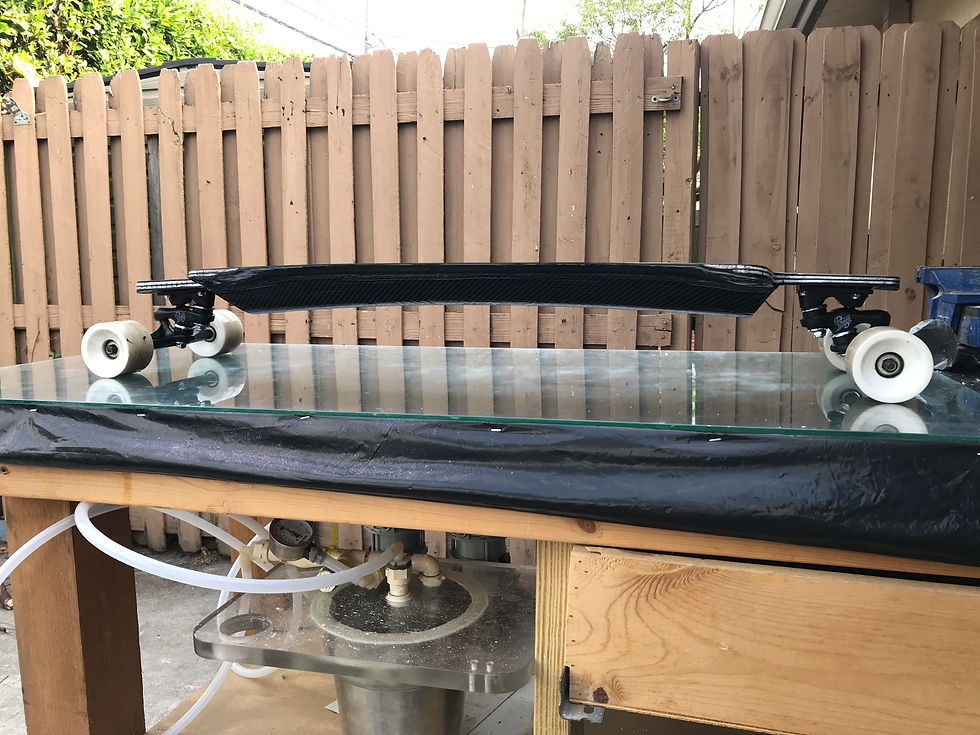

I chose a medium finish peel ply and it makes great grip "tape". It is also easily replaceable.

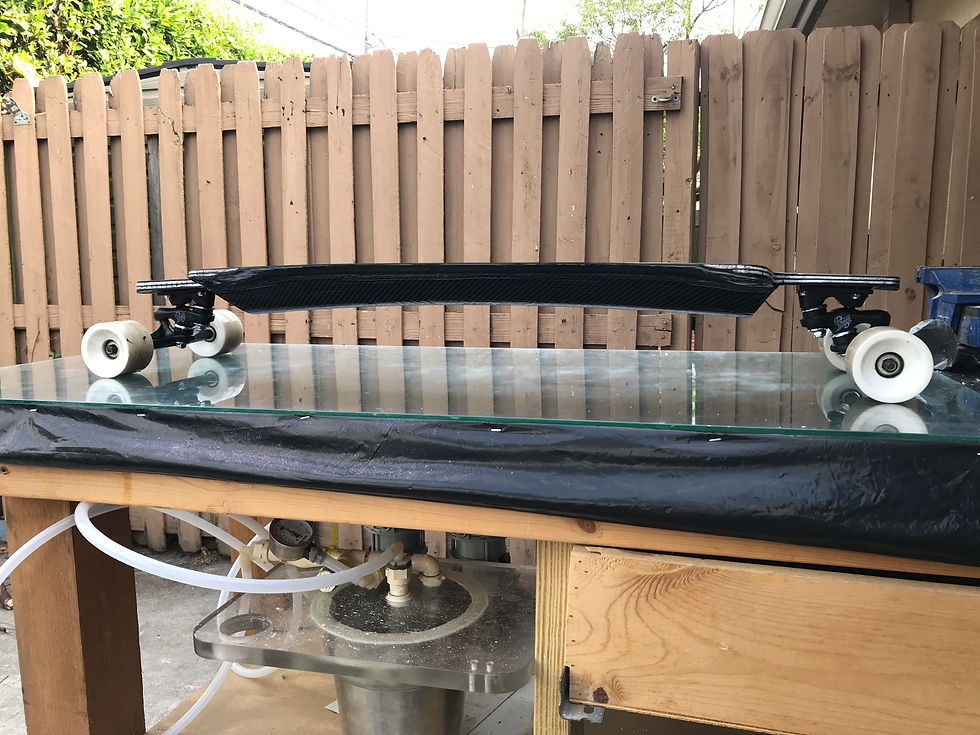
During the recent Covid-19 lockdown I had the opportunity to explore a design concept that I have had in my mind for many years. My motivation for the project (besides cabin fever) was the Rock West Composites Design Competition. Hollow beams and specifically hollow composite beams are very commonly known for their light weight, high strength, and stiffness attributes. Bicycles, airplanes, sailboat masts and many other high performance and weight sensitive vehicles have capitalized on the advantages available from this structure. But as far as my research can find, no one has ever used this design on a longboard. Lightweight, strength and stiffness are all key attributes of a good downhill machine. Flexibility does help improve comfort when pushing along the sidewalk, but when you're traveling at high speeds on steep hills, this is where the stiffness of the board gives you the confidence to push harder and go faster. Carbon fiber is also the most forgiving composite material to stress cycles, with little to no work hardening during flexural cycling (corning in this case) and high resistance to impact forces (bumps). Overall these prototypes were a success. The boards weigh just over 2 pounds on their own and are 40"x 9" in size. My proof of concept was done with a minimal budget and the removable silicone molded core for molding the beam interior worked well.
Solar Panel Arrays

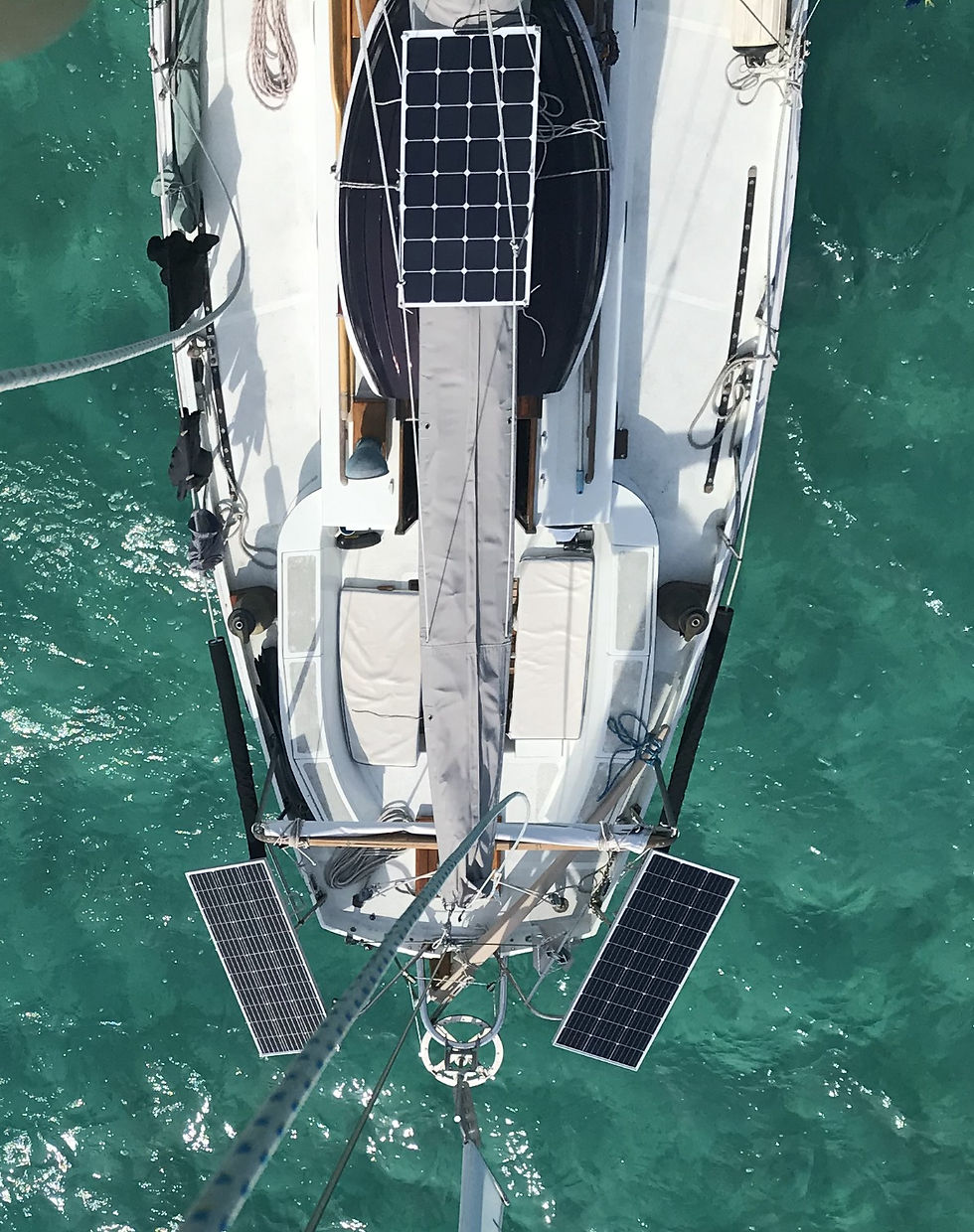


Solar panel and controller technology are advancing rapidly and are becoming fairly ubiquitous at the same time. But when attaching a solar charging system to a moving vehicle and expecting it to deliver the power needed for that vehicle's amenities, battery bank and in the space available, there is always a unique design challenge at hand. We have used solar power systems on 4 of our own travel machines, Sunny (teardrop trailer), Desiderata (sailboat), Sirocco (sailboat), KOKO (Airstream camper). Each one has been a learning experience with pluses and minuses intrinsic to that machine. Power demands and available space are the top contenders in defining the system, while budget, and secondary available charging sources round up the design brief. I have a strong understanding of the principles needed to create a successful solar charging system to be applied to a project. It's a combination of dedicated research and understanding of the available technology as well as first hand experience.
Small Stuff


These worked flawlessly and added a touch of classic class to Solvi.

The finished replacement tip of milled fiber and chop fiber reinforced epoxy. The surface was easily filled/faired and painted to match. This spreader tip has seen over 4,000nm of use without trouble.

Some of my favorites from the last couple years.
Windvane

This is immediately following the bolt up and assembly of the wing sail. It weather vanes very responsively. We have now put over a 1,000nm on this vane and it has changed our life underway dramatically for the better. We now consider a good working windvane absolutely necessary for offshore passage making. It makes for a far safer boat.

The original wing sail frame drawing for the build. This design was slightly modified to accommodate solar panels and improve the wind quality over the sail by raising it 15".

The wing sail bearings blocks are self aligning dual angular contact Delrin with 316 bearing balls. Working load on the each block is 240lbs.

This is immediately following the bolt up and assembly of the wing sail. It weather vanes very responsively. We have now put over a 1,000nm on this vane and it has changed our life underway dramatically for the better. We now consider a good working windvane absolutely necessary for offshore passage making. It makes for a far safer boat.
A custom trim tab windvane for our classic cruising cutter. Based upon the "Freehand System" built by Mike Anderson for the Lyle Hess designed Bristol Channel Cutters.
Intrepid 410 Evolution

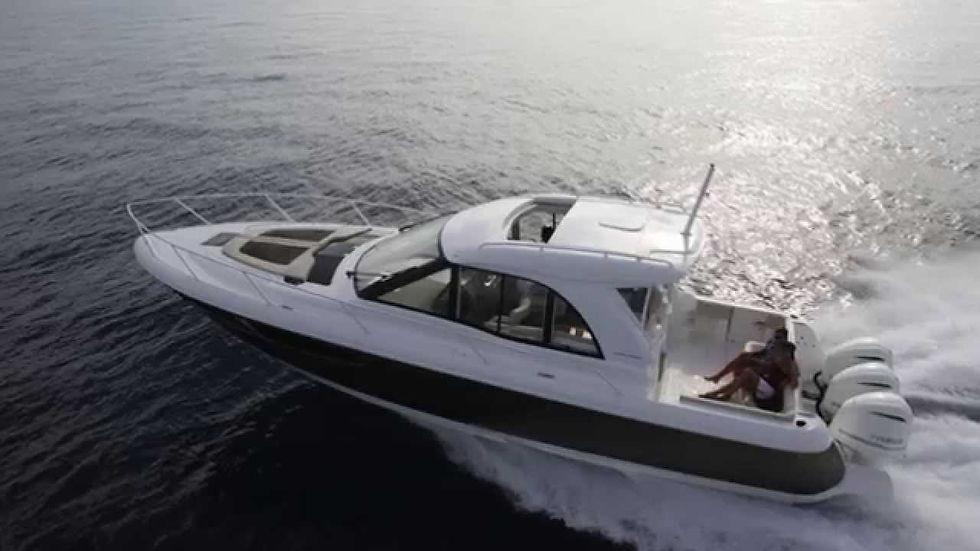


I was given a great opportunity to work with a very talented manager on (at the time) Intrepid Powerboats newest project. The 410 Evo, had the biggest composite parts and the most complicated systems they had ever tried as a company. For being the company's first cabin cruiser, the engineers did a great job. Primarily just Luis and myself for hulls 1 and 2 assembly, there were a thousands problems to solve, with systems layouts, and new parts to design and build on the fly. It was very instructive for me to work with such an experienced engineering team and manager. I then led the training of hulls 3 and 4 through the production line.
For questions or comments regarding this page: